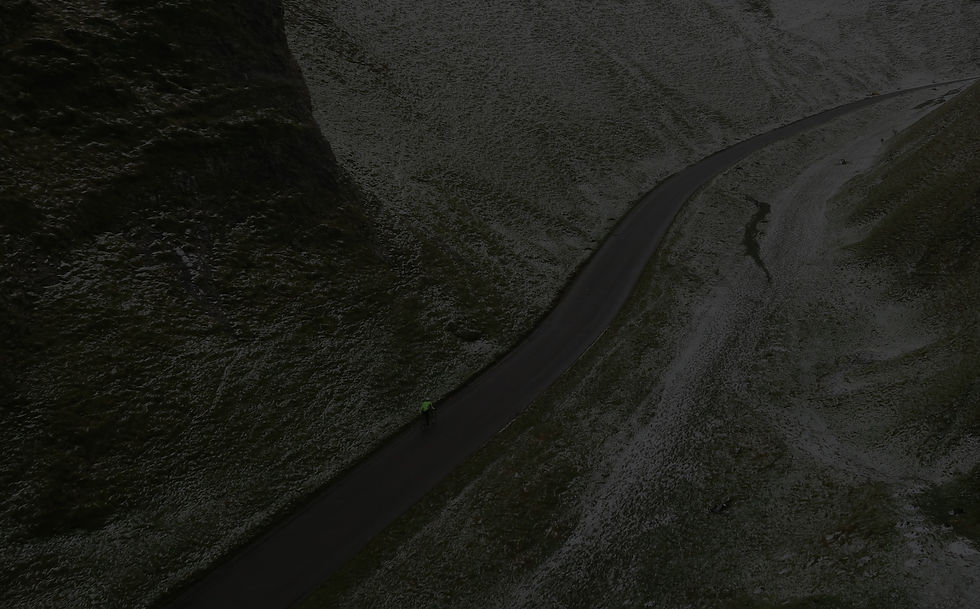
MA3™ Refrigeration Technology
Modified Aqua-Ammonia Absorption ("MA3™") is a refrigeration technology providing ammonia chilling as cold as -75ºC at a chiller operating pressure of 5 kPa absolute.
Compared to conventional refrigeration systems, the MA3™ process reduces the scope of overall mechanical rotating equipment required, resulting in significant capital and operating cost savings.
MA3™ is patented in 17 countries and patent-pending in over 40.
Applications
ssCCUS
Refining & Petrochemicals
Blue Hydrogen
Food Processing & Flash Freezing
ssLNG
NGL Extraction
Fuel Gas Conditioning
CO2 Liquids
Industrial Refrigeration
Gas Processing
Benefits of MA3™
MA3™ is thermally driven, meaning Cool can capitalize on opportunities to co-locate at industrial facilities with waste heat, significantly reducing project costs and environmental impact. Other benefits include:
-
Reduced operating and maintenance costs due to low shaft horsepower requirements.
-
Lower upfront capital costs due to the elimination of expensive turbo expansion equipment and use of less mechanical rotating equipment.
-
Easily adoptable with no specialized equipment (all necessary components are "off the shelf") or training required to operate.
-
Highly flexible with an operating turndown ratio of 10:1 (MA3™ can operate efficiently at as low as 25% capacity).
How MA3™ Works
(I)
(II)
(III)
(IV)
Almost pure liquid ammonia is vaporized in the ammonia chillers (starting at the top box in process diagram).
The ammonia vapor is routed to the top of the VAT™ and contacts the lean solution. The ammonia vapor absorbs into the lean solution at sub atmospheric pressure until reaching saturation. As the ammonia is absorbed by the lean solution, the ammonia content of the solution increases, creating a rich solution. As the aqua-ammonia solution builds head within the VAT™ multiple stages of chillers can introduce additional ammonia into the VAT™ resulting in additional chilling.
The Rich Solution Pump transfers the solution to the rectification column for regeneration.
Heat energy is used to recover the ammonia from the now-rich aqua-ammonia solution. Ammonia vapor is produced within the rectification column as well, producing the lean solution.
-
The ammonia vapor is condensed and cooled into the liquid that is flashed to sub-atmospheric pressure to the chiller to be used for cooling the process gas.
-
The subcooled lean solution is throttled to sub-atmospheric conditions to the top of VAT™ for contact with the ammonia vapor.


MA3™ ssCCUS
Cool has developed amine-based post-combustion carbon capture using MA3™ for liquefaction of CO2. For industrial applications where the raw CO2 stream is greater than 85%, the MA3™ system may be configured to directly "Chill and Distill™" the CO2 into a liquid form without the need for an amine-based system.
To dispose of CO2 from an amine system into a pipeline, CO2 must be in the dense phase at ~2200psi. To achieve this pressure, conventional CCUS systems use multi-stage compression.
How MA3™ ssCCUS Works:
MA3™ ssCCUS compresses CO2 to 230psi, then dehydrates and liquefies the CO2 stream before pumping to the dense phase. This process provides optionality for disposal:
-
Truck liquefied CO2; or
-
Pump liquefied CO2 into a pipeline.
Amine systems with MA3™ have advantages of turndown flexibility, lower capital and operating costs, and heat integration between the amine system and MA3™.
Cool is targeting ssCCUS projects producing 50 - 400 tonnes CO2 per day (~20,000 - 150,000 tonnes per annum).
MA3™ Amine-Based ssCCUS

MA3™ Chill and Distill™
Chill and Distill™ is ideal for applications such as power generation, process heaters, and industrial processes.

DPLC™ ssLNG & NGL Extraction
Cool's Dense Phase Liquefaction Cycle ("DPLC™") is a process for NGL extraction and to produce LNG using stationary cryogenic equipment and MA3™ technology.
How DPLC™ Works:
Inlet gas runs through a booster compressor and is then treated to remove CO2 and H2O. The pressurized gas then joins a stream of recycled gas, returning via two heat exchangers and a recycle compressor.
The commingled gases then pass through an initial heat exchanger and an ammonia chiller, which cools the gas to approximately -70ºC using the MA3™ process.
From the ammonia chiller, the chilled gas passes through a second heat exchanger and is throttled through a Joule Thomson valve into a separator, where approximately half of the gas liquefies into LNG which is then held in storage.
The remaining cold gas is then recycled through both heat exchangers, the recycle compressor and subsequently commingled with the inlet gas stream, from where the process continues.
Using DPLC™, Cool is targeting ssLNG projects to produce 50,000 - 200,000 USG/d per train.
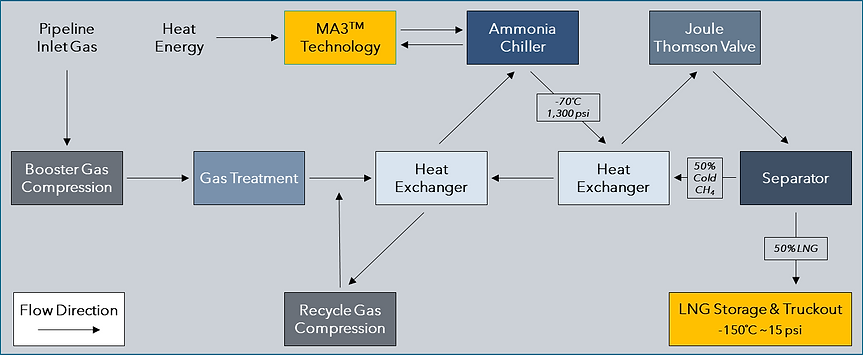
External Review of Technology
Since 2016, Cool has successfully operated a pilot plant in Southeast Calgary.
In October 2017, Jacobs Consultancy Inc. completed a review of the MA3™ refrigeration technology at the pilot plant concluding that:
-
“The technology is well suited for small to mid-scale LNG production applications”;
-
“The technology has been developed sufficiently to warrant scale-up to commercial operations”; and
-
“The DPLCTM LNG liquefaction configuration is targeting the small-scale regional LNG market… However, this refrigeration technology could have many other possible commercial applications.”
The review identified modifications to the pilot plant for a “path forward” to enhanced functionality, which were subsequently implemented in 2018.
Cool has successfully stopped and started the plant 100s of times in operating temperatures ranging from -30°C to +30°C.
